Poly Bagger
|
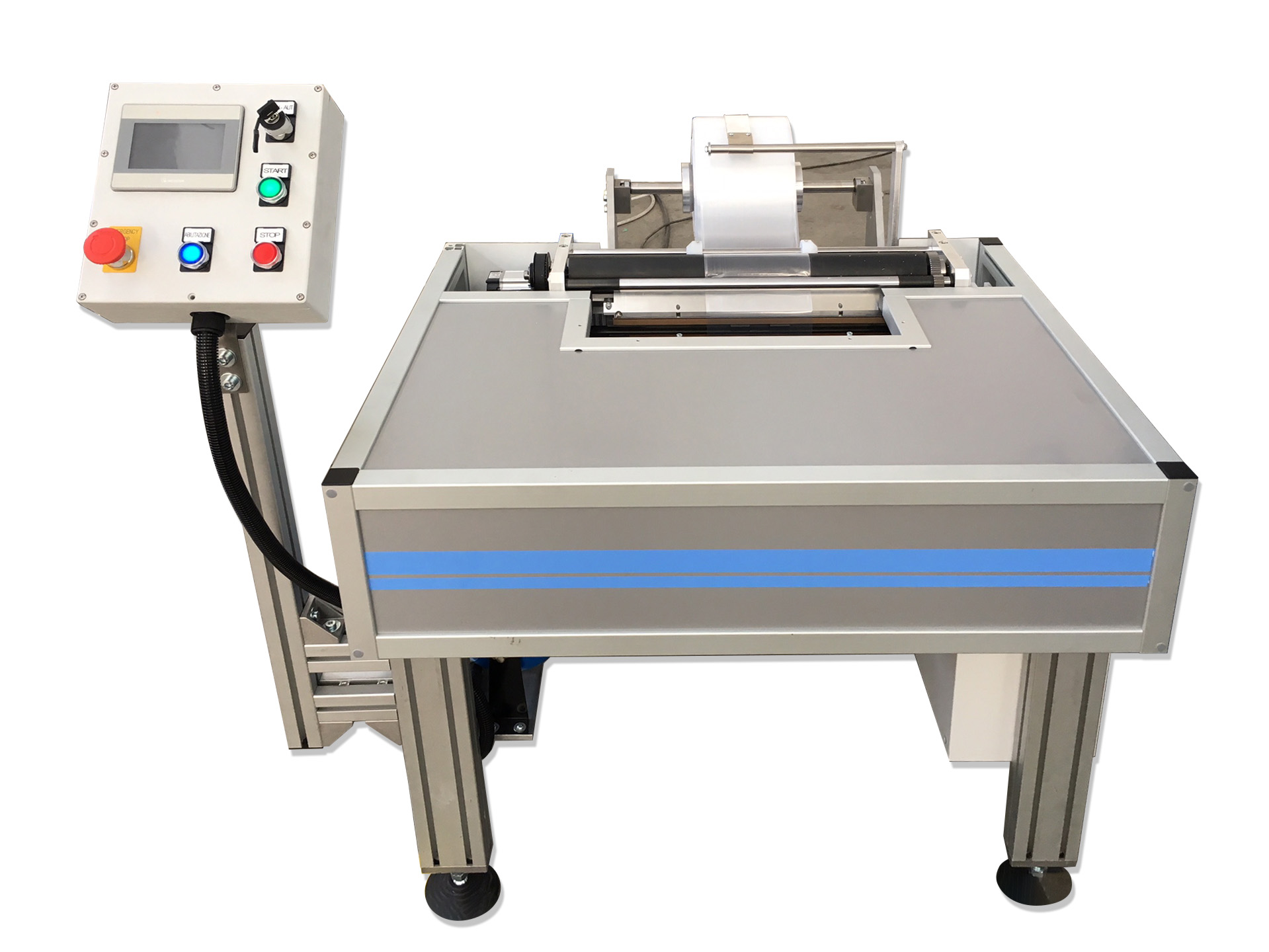 |
BP-110
Ultra-compact poly bagger using tubular film to create bags of preferred length. The machine can be integrated with a scale or counter or it can go directly under a sorting machine to bag hardware straight out of the sorting process, fully automatically. Can also use printed film
|
- Touch Screen HMI
- Programmable Bag Length
- Seal by Electrical Impulse
- Manual or Automatic Loading
- Flat Bag Size Range: 4” - 12” Width 4” - 12” Length
- Bag Tube Material: 2 - 4 mil
- Maximum OD of Film: 10” (3” ID)
- Speed Range: 3 - 6 BPM
- ACCESSORIES:
- Code printing device
- Hanging hole device
- Printed film registration
|
|
Vertical Form, Fill & Seal Machines (VFFS)
|
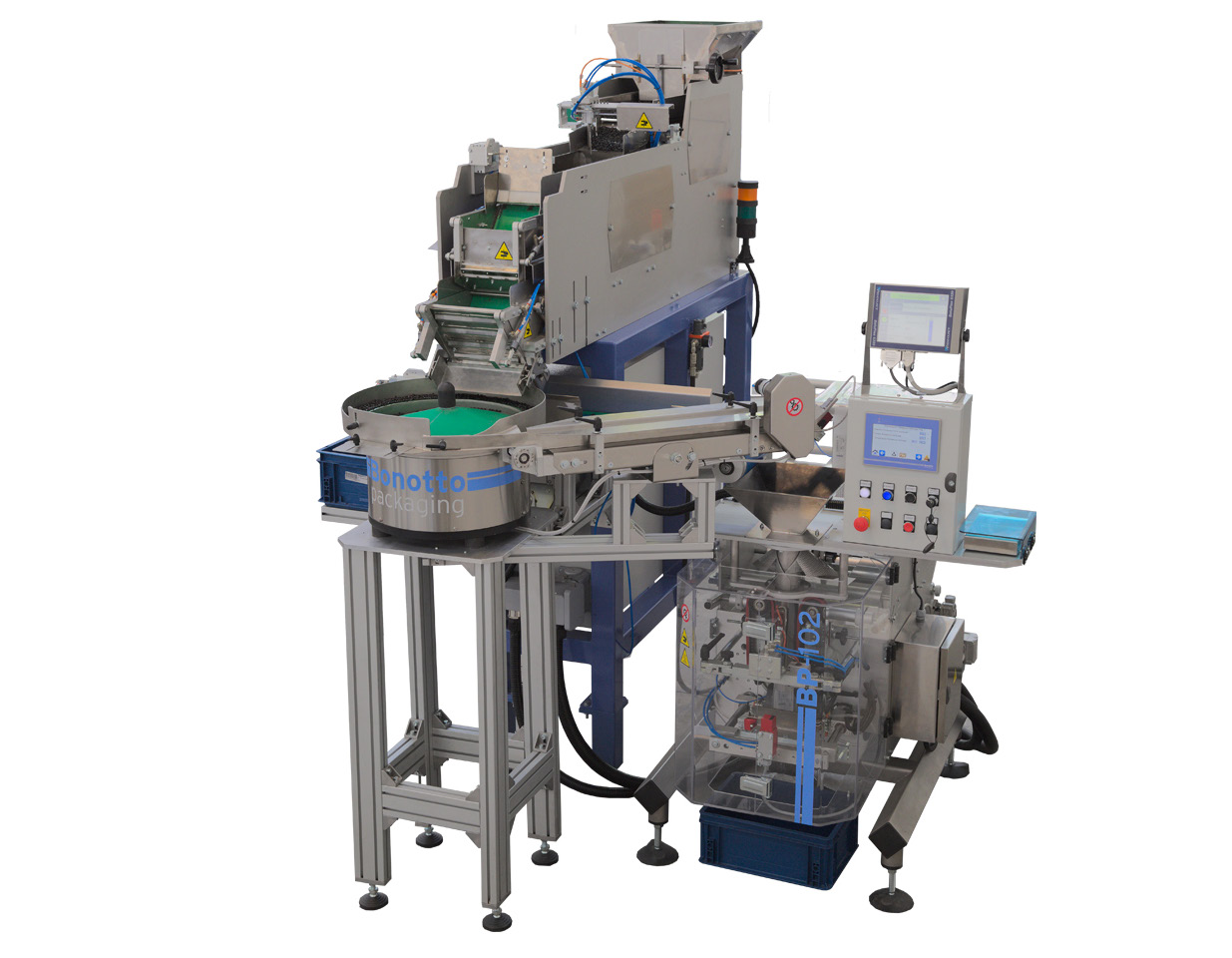 |
BP-102/104
Designed to package hardware or any free-falling bulk products. They can be integrated with automatic production lines and be synchronized with automatic feeding, counters and scales.
|
- Anodized aluminum side frame with adjoined electrical cabinet.
- The motor-driven film unwinds by toothed belts.
- Bag length regulated by an encoder.
- Double cycle film unwinds to make long bags.
- Available in PE or heat seal-able material version.
- Available in inclined version 45°.
- Machine built according to CE standards.
- PLC controlled.
- HMI touch screen Hakko.
- BP-102 Max flat bag 175 mm by 300 mm length.
- BP-104 Max flat bag 270 mm by 400 mm length.
- ACCESSORIES:
- Print on film systems
- Heavy product bag support
- Chain package
|
|
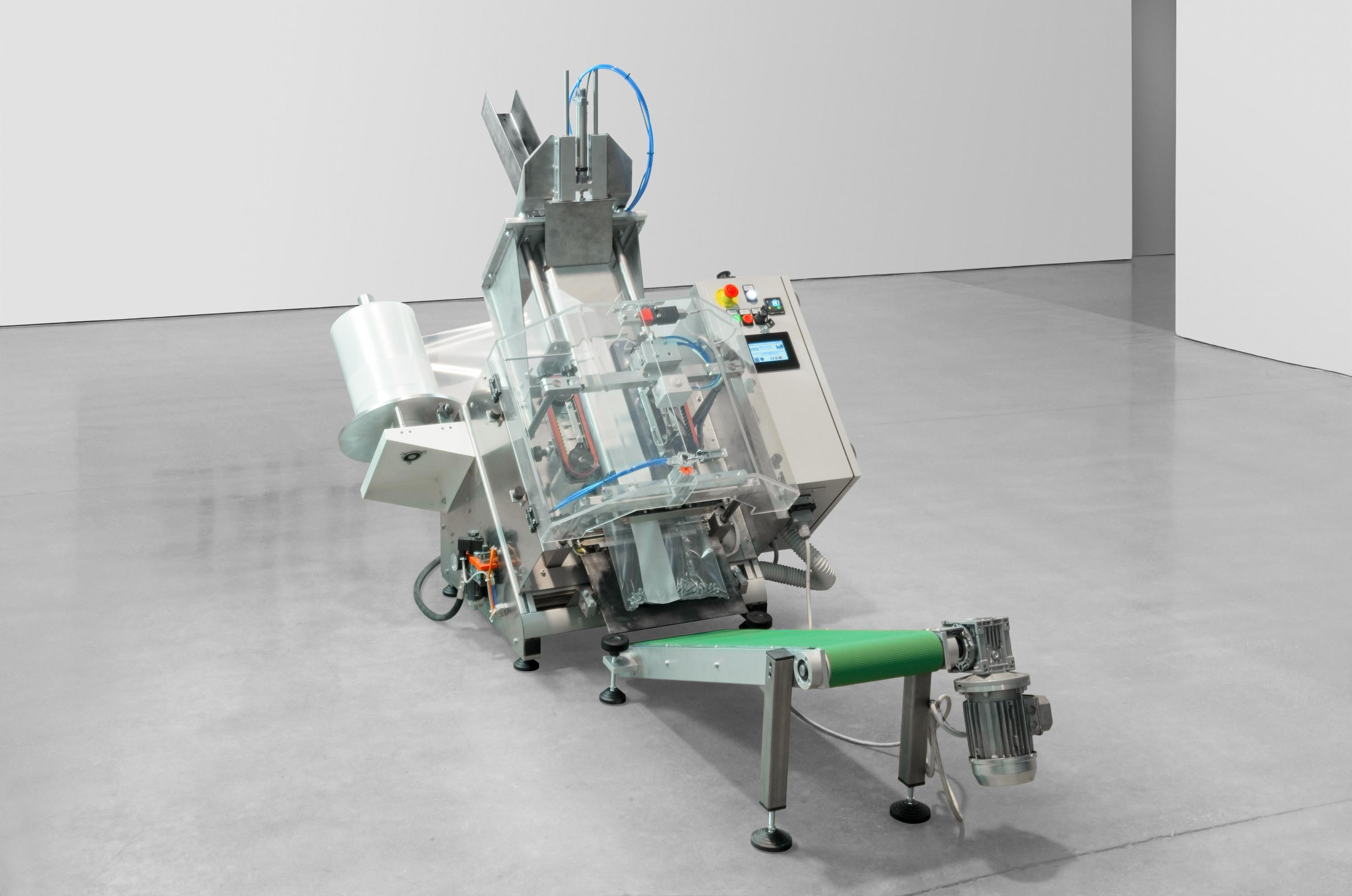 |
BP-109/I
The BP-109/I Inclined form-fill-seal machine can be integrated into automatic production lines and synchronized with automatic feeding devices, weigh/count scales, parts counting systems, sorting and inspection machines.
|
- Rectangular forming tunnel: Min 60 x 80 mm – Max 180 x 105 mm.
- Reel holder for pre-folded film
- Package weight up to 10 Kg
- Motor-driven film feed belts
- PLC controlled
- Bag length check by an encoder
- Band sealing for PE film
- Double bag length check
- Machine built according to CE standards
- Support for heavy bag with vibration.
- FILM: PE Polyethylene
- FILM WIDTH: pre-folded film min 150 max 300 mm
- BAG WIDTH: 140 - 280 mm
- BAG LENGTH: 150 - 240 mm, with double seal 450 mm
- SPEED: up to 5 bags/minute
|
|
Weigh/Count Scale
|
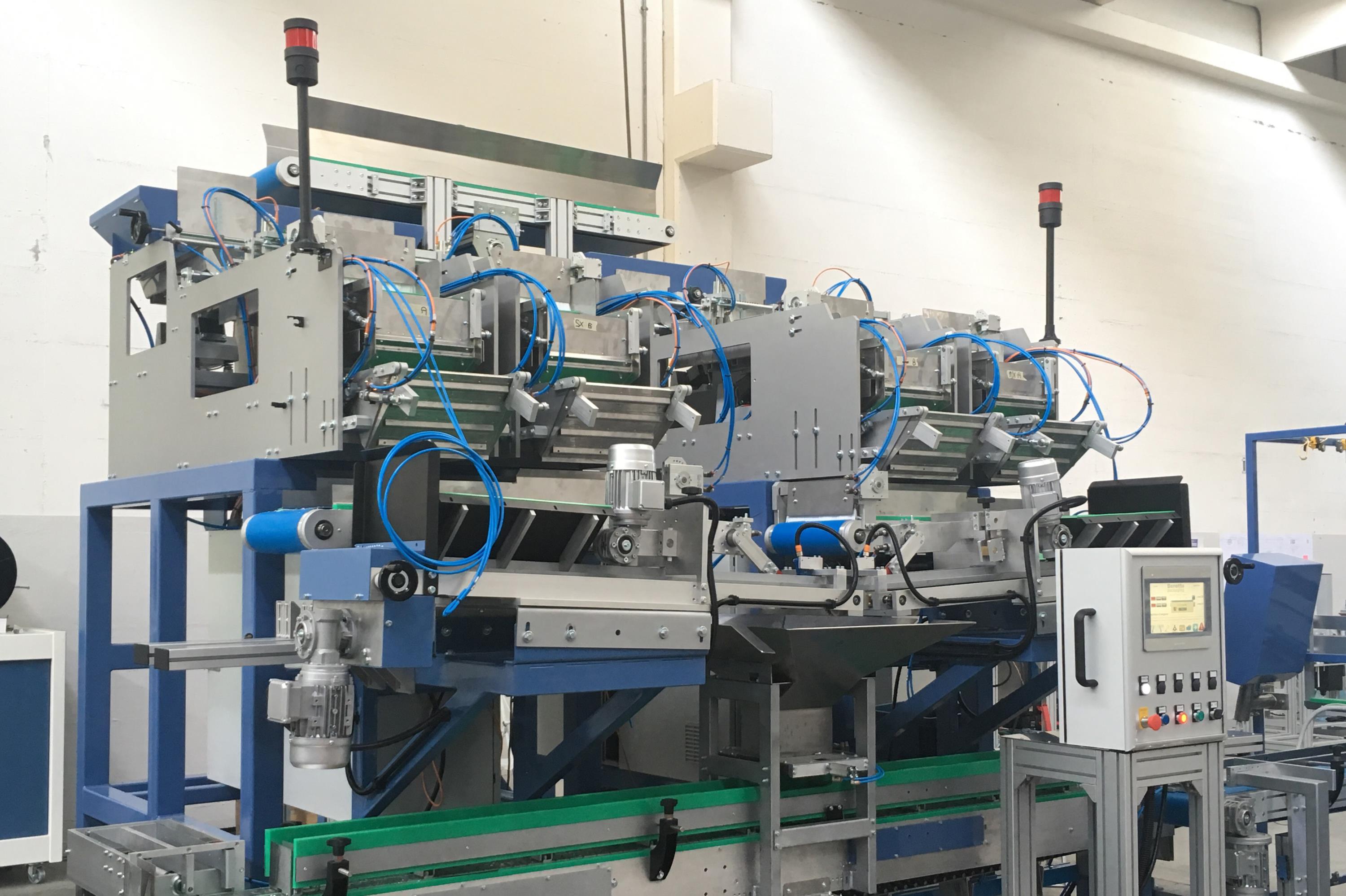 |
BP-305
The PLC controlled BP-305can weigh and count medium size hardware such as screws and bolts. The parts are dosed from bulk and can then be dropped into a bagger or a box, depending on the application.
|
- Twin machine.
- Anodized aluminium side frame.
- N.2 60-litre hopper capacity.
- Pre-feed vibrating chute controlled by a mobile scale or photocell.
- N.2 Bulk-feed vibrating chute with pneumatic controlled closing flap.
- N.2 Weighing baskets with double gates to dump the products into the feeding conveyor or into the roller fine feed unit.
- N.1 Unit counting system with roller feeder controlled by DC motor.
- Weighing head with mechanically protected loading cell to offset any accidental overloads.
- Possibility to store different programs to suit various products.
- Machine built according to CE standards.
- WEIGHT RANGE: From 1000 g to 18000 g
- PRODUCT RANGE: Screws min diam. M6 min length 15 mm
Bolts max diam. M22 / max length 150 mm
- SPEED: Up to 10-15 dumps per min.
- WEIGHT BASKET SENSITIVITY: 5-10 G
|
|
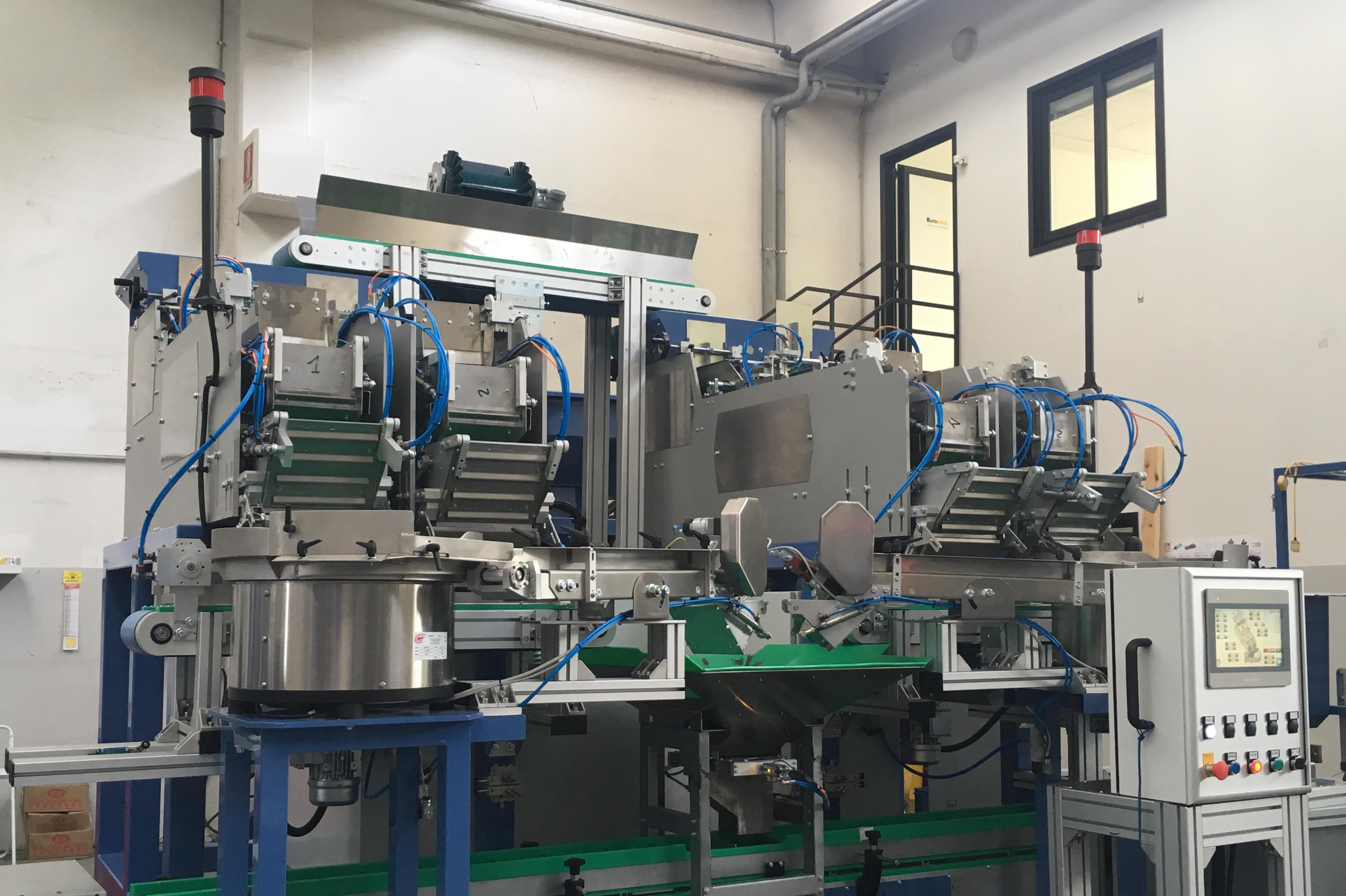 |
BP-306
The PLC controlled BP-306 system can weigh and count small, medium and large size hardware such as nails, screws, bolts, plastic or aluminum casts and small parts in general. Parts can then be dropped into a bagger or a box.
|
- Twin Scale
- Anodized aluminium side frame.
- N.2 60-liter hopper capacity.
- Pre-feed vibrating chute controlled by a mobile scale or photocell.
- N.2 Bulk-feed vibrating chute with pneumatic controlled closing flap.
- N.2 12-liter weighing baskets with pneumatic opening.
- N.2 Staging baskets with double gate to dump the products into the counting unit's vibratory bowl
- Weighing head with mechanically protected loading cell to offset any accidental overloads.
- Counting unit with photocell and synchronization basket.
- Possibility to store different programs to suit various products.
- Machine built according to CE standards.
- WEIGHT RANGE: From 500 g to 7000 g
- PRODUCT RANGE: Small, medium and large size hardware
- MAXIMUM PRODUCT LENGTH: 90 mm
- SPEED: Up to 20 cycles per min.
|
|
|
BP-309
The PLC controlled BP-309 scale is ideal for counting and weighing small and medium-size hardware such as nails, screws, nuts, bolts, plastic and aluminum casts and small parts in general. Parts can then be dropped into a bagger or Carton.
|
- Tubular 4" steel frame, painted
- High sensitivity weight cell for precision dosing
- 500 mm vibratory torsional feeder for fine feed
- Vibrating plate for gross feed with electromagnet
and harmonic steel springs
- Adjustable vibrating speed by electronic card
- Touch screen HMI and programmable recipes
|
|
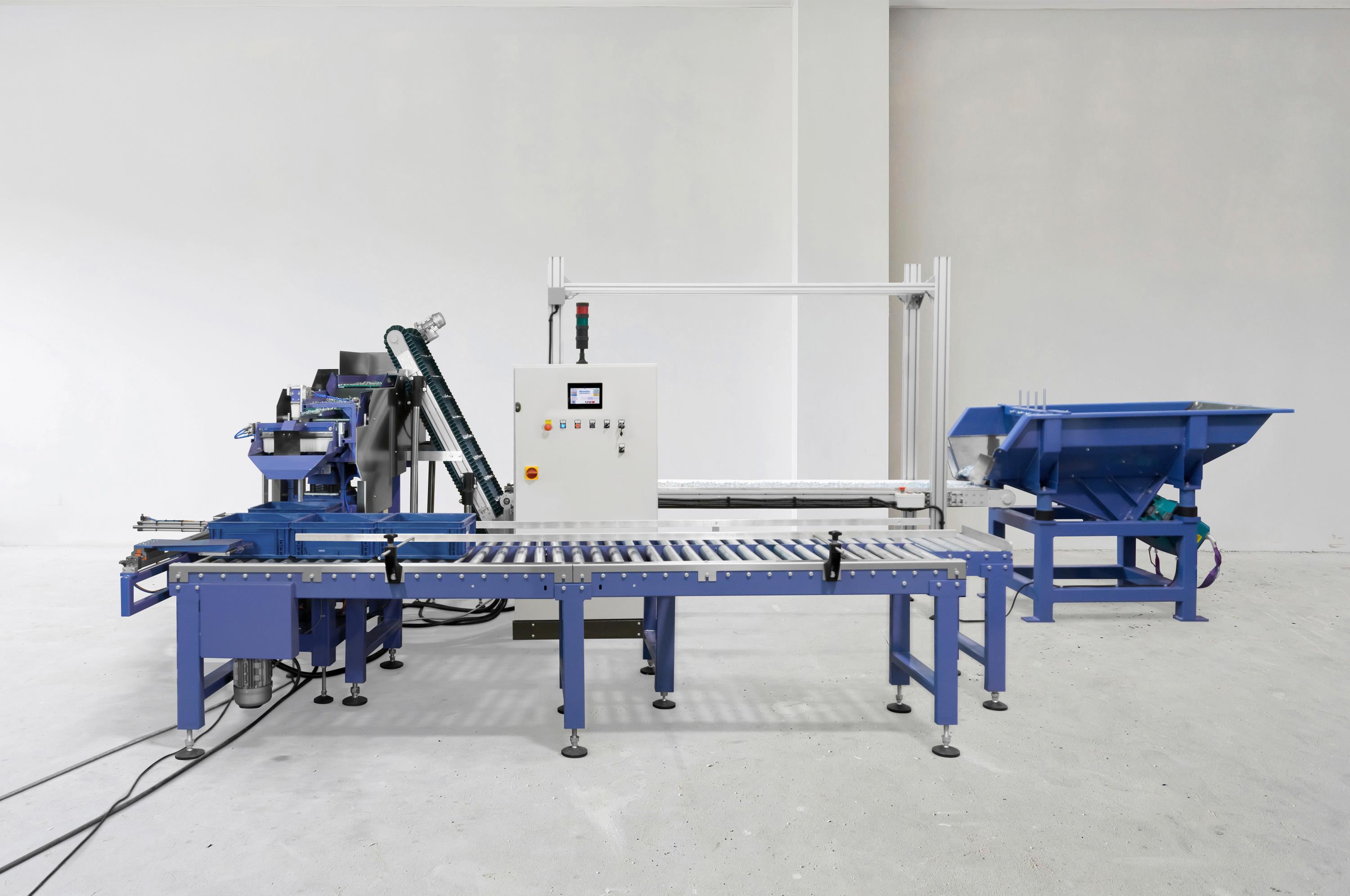 |
BP-310
The PLC controlled BP-310 scale is ideal for counting and weighing small, medium and large size hardware such as nails, screws, nuts, bolts, plastic and aluminum casts and small parts in general.
|
- Pre-feed vibrating chute controlled by photocell.
- Bulk feed vibrating chute with pneumatic controlled closing flap.
- Fine feed vibrating chute with pneumatic controlled closing flap.
- Possibility to store different programs to suit various products.
- Machine built according to CE standards.
- WEIGHT RANGE: From 5 Kg to 30 Kg
- PRODUCT RANGE: Small, medium and large size hardware
- MAXIMUM PRODUCT LENGTH: 150 mm
- SPEED: 1-3 batches per min
- WEIGH BASKET SENSITIVITY: 10 g
|
|
Carton Former
|
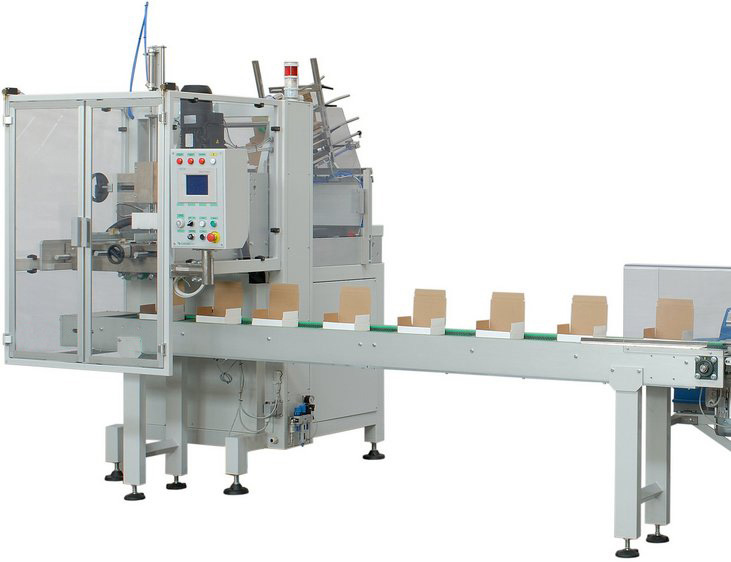 |
BP-402
The carton former BP-402 forms flat cartons to create boxes with or without cover. The machine is equipped with a carton magazine unit with an automatic arm that grabs flat cartons from the magazine with suction cups. It then uses a hot glue spraying device for gluing flaps if needed. The boxes, after being formed with a replaceable forming head, travel on an exit conveyor to go to the filling stations.
|
- Painted steel construction.
- Magazine with automatic arm using suction cups with Venturi system
- Box assembling through hot-melt glue application or tuck-in closing.
- Former's mold with electrical axis
- Fully adjustable female mold by manual hand-wheel
(applicable to all formats).
- PLC controlled.
- Machine built according to CE standards.
- FORMED BOX DIMENSIONS:
- Min 100 x 80 x 25 mm
- Max 450 x 300 x 100 mm
|
|
Top Loading Case Packer
|
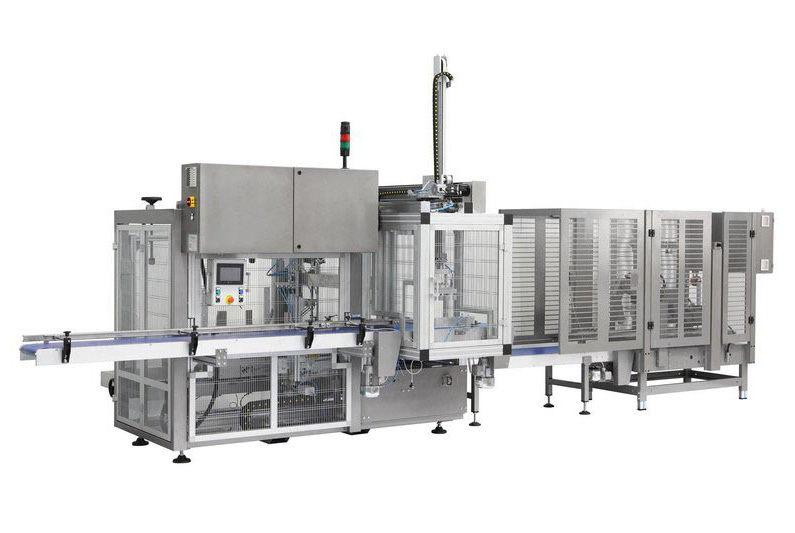 |
BP-503
The top-loading case packer BP-503 forms a carton securing it with tape on the bottom. The carton is then moved to the filling station where products are placed in the b by a picking head equipped with suction cups and /or pneumatically operated holders.
|
- Painted steel construction.
- Electro-pneumatic functioning.
- Size-change adjustments by hand-wheels.
- PLC controlled.
- Lower flap closure with either tape or hot melt glue.
- Machine built according to CE standards.
- Carton magazine with suction cups picking arm.
- Product conveyor belt with variable speed controlled by inverter, and stop function to separate the product.
- Pneumatic compacting device.
- By-pass device for product unloading.
- Centering funnel.
- Pick-up head with vacuum or pneumatic pliers.
- Top loading movements controlled by integrated PLC.
- FORMED BOX DIMENSIONS:
- Min 250 x 150 x 120 mm
- Max 600 x 400 x 400 mm
|
|